The CO2 gas shielded welding machine is a machine, electric and gas integrated device. In the use process, problems occurring should be understood, analyzed and solved from three aspects. Generally, not welding as circuit fault, not welding well as mechanical fault, welding poorly as process problem or protection gas impurity, gas path problem and other reasons. This is the epitome of experience, while the latter two account for 90% of the total problems.
When users encounter unstable arc, poor welding effect, and other abnormal phenomena, do not prematurely determine that the CO2 welding machine has failed. The occurrence of these problems or abnormal phenomena is often due to the following factors: fuse melting, loosening of fastening parts, forgetting to turn on the switch, improper parameter adjustment, cable breakage, gas hose cracking and air leakage, damage to the CO2 welding gun, etc. These faults and abnormal phenomena can be eliminated by the user himself. If you encounter a circuit fault that cannot be eliminated, you can go to the local sales network for after-sales treatment. Now I will explain to you the problems that are easy to encounter in the welding process, the defects that are easy to produce in the weld seam and the preventive measures.
Pore
Causes (generally have nothing to do with the welding machine itself)
1. Damage or freezing of the flowmeter of the gas regulator;
2. The value of the gas flow setting is not matched;
3. The fault of the welded torch body;
4. The solenoid valve fails;
5. There are oil, dirt, rust, paint film or welding wire for too long;
6. The surface of the welding wire has rust or other quality defects.
Prevent measures
1. Replace the flow meter or heated the gas flow meter;
2. Adjust to the appropriate air flow value;
3. Replace the welding torch;
4. Replace the solenoid valve;
5. Clean up the surface of the mother material, the welding wire extends to the appropriate length ;
6. Replace the new welding wire.
Welding current is unstable
Causes
1. The input and output cable is too long and detailed caused by the current instability;
2. The phenomenon of damage and wear of the wire delivery mechanism;
3. The aging of the filament hose;
4. welding gun head Severe (or incorrect pores).
5. Severe wear of the conductive tuling (or the pores are wrong).
Prevent measures
1. If input and output cables are too long, use cables with larger wire diameters;
2. Replace the new wire sending mechanism;
3. Replace the new silk hose;
4. Replace the new welding gun head;
5. Replace the new guide mouth.
Sending silk instability
Causes
1, the wire hose resistance is large;
2.Improper adjustment of wire feeding pressure;
3, poor welding wire, welding wire cross, uneven diameter or hard bending;
4, the conductive nozzle specification is wrong or the inner diameter is too small;
5, the wire wheel has dirt;
6. The bending radius of the welding torch cable is small, and the bending radius should be greater than 300mm.
Preventive measures
1, clean the wire hose with compressed air or replace the wire hose;
2, adjust the pressure arm, select the appropriate wire feeding pressure;
3, choose good quality welding wire;
4. Select a conductive nozzle that matches the diameter of the welding wire;
5. Clean or replace the wire feed wheel in time;
6, welding as far as possible to make the torch cable straight.
Arc instability
Cause
1, the output voltage is unstable;
2. Unstable wire feeding;
3. 3, poor welding wire quality;
Preventive measures
1, try to keep the dry elongation of the welding wire unchanged;
2.Check wire feeding during welding to ensure smooth wire feeding;
3, select good wire quality welding wire;
The welding wire is glued to the conductive nozzle
Cause
1, the extension length of the welding wire is too small;
2, the gas flow is too small;
3, the spatter in the nozzle is not cleared in time;
4, welding parameters do not match.
Preventive measures
1, choose the appropriate dry elongation;
2, adjust the appropriate gas flow;
3, timely clean the spatter in the nozzle;
4, select the appropriate and matched welding parameters.
Welding spatter is large
Cause
1, welding current and voltage do not match;
2, the inductance does not match, the greater the general current the greater the inductance;
3.The welding wire is extended too long or too short;
4.There are rust and oil stains on the surface of the base metal and welding wire.
Preventive measures
1, adjust the matching current and voltage values;
2, adjust the appropriate inductance value according to the current;
3, choose the appropriate dry elongation;
4, clean the surface of the base metal or replace the new welding wire.
Crack in weld
Cause
1, welding wire or workpiece is not clean;
2, the quality of welding wire is not good;
3, the first welding seam is too thin;
4, the current and melting depth is too large.
Preventive measures
1, replace the new wire, clean the surface of the workpiece;
2, select good wire quality welding wire;
3, increase the width of the weld;
4, adjust the welding specification, control the penetration.
A serpentine bead appears during welding
Cause
1, the conductive nozzle wear seriously;
2.The conductive nozzle is loose;
3. The mouth of the wire feed tube is too large;
4, the dry elongation of the welding wire is too large;
5, welding wire straightening adjustment is not good.
Preventive measures
1, replace the new conductive nozzle;
2. Tighten the conductive nozzle;
3, regular maintenance and cleaning of wire feeding tube or replacement of new wire feeding tube;
4, choose the appropriate dry elongation;
5, adjust the scale of the pressure arm, choose the right pressure.
Lack of penetration
Cause
1, the welding current is small, the melting depth is shallow;
2, groove and gap size is unreasonable, blunt edge is too large;
3, the arc is too long;
4. Poor cleaning between layers and welding roots.
Preventive measures
1, adjust and select the appropriate welding current;
2. The design of groove and gap size should be reasonable.
3. Reduce arc length;
4. Clean the layers and welding roots.
Weld through
Cause
1, welding current is too large;
2, the welding parts heated too much;
3, the groove butt clearance is too large;
4, welding speed is slow, arc residence time is long, etc.
Preventive measures
1, select the appropriate current parameters;
2, when heating the welding parts, pay attention to the temperature should not be too high;
3, groove and clearance design should be reasonable;
5. Speed up the welding speed appropriately.
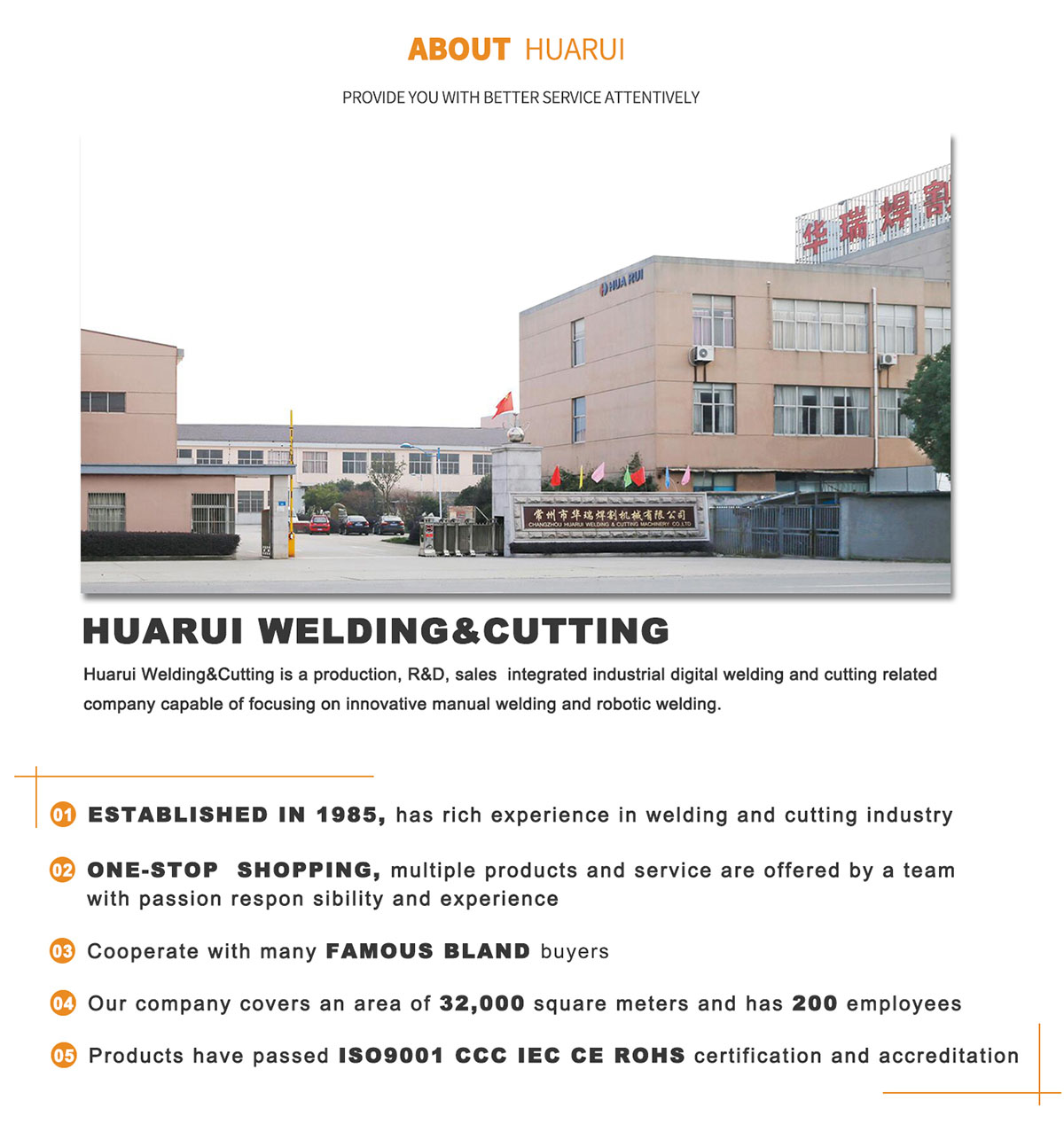
HUARUI alibaba shop:
https://topwelding.en.alibaba.com
https://czhuarui.en.alibaba.com
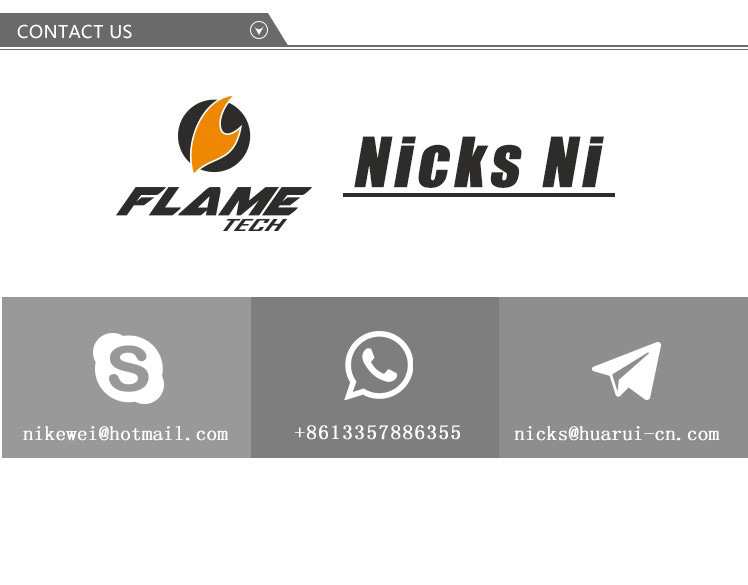